Backflow Education
Welcome to BSI’s Backflow Academy, where we provide comprehensive training and resources to help you master the complexities of backflow program management. Whether you are a professional in the water industry, a property manager, or a business owner, our academy equips you with the knowledge and skills needed to navigate the intricate regulations and technical aspects of backflow prevention. Through practical insights and up-to-date compliance guidance, Backflow Academy empowers you to protect your water systems effectively, ensuring safety and compliance at every step.
What is Backflow?
Typically, water will flow from the public water supply to the consumer’s plumbing distribution system. Backflow is the undesirable reversal of this flow of water and undesirable substances from the non-potable source to the potable source.
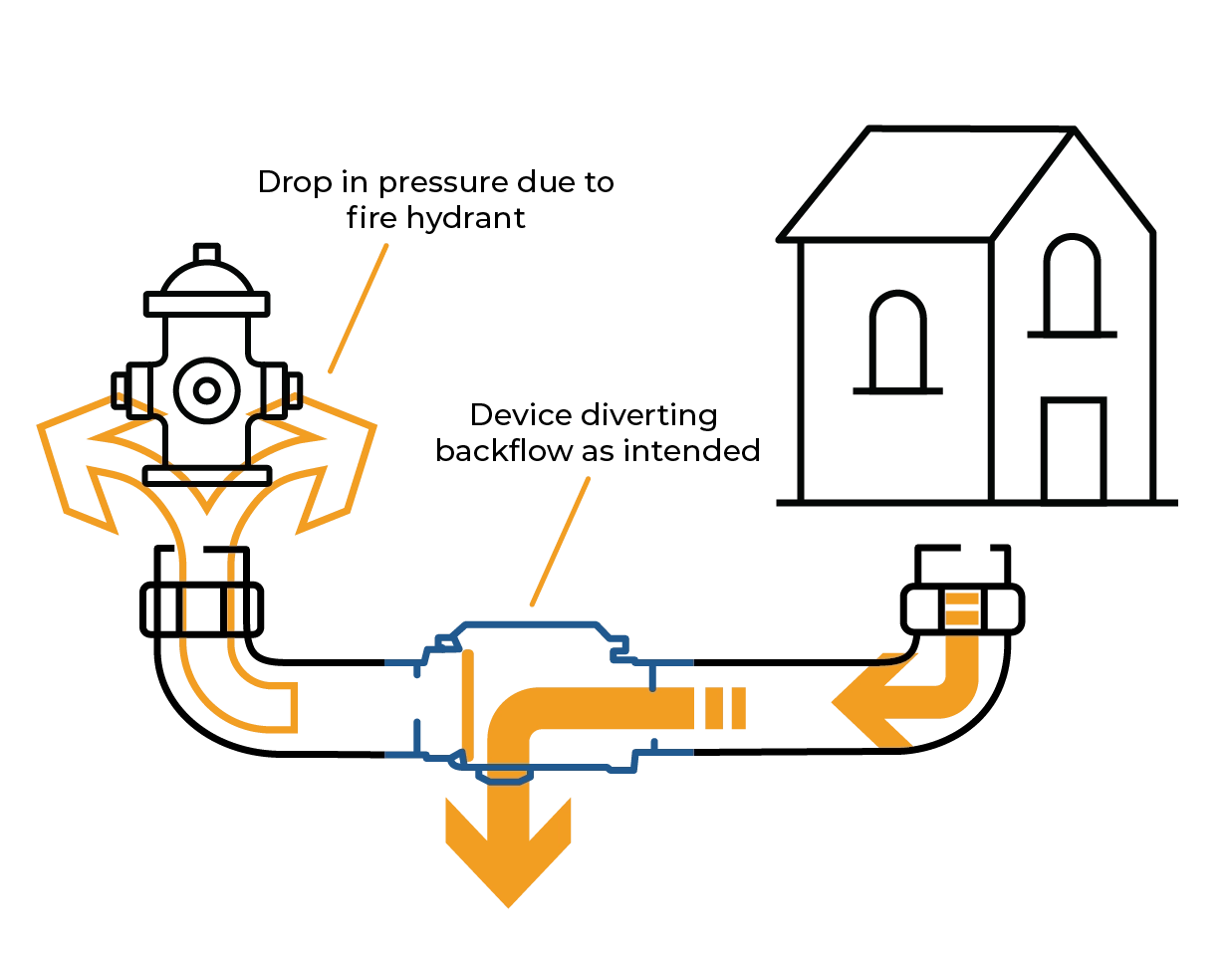
Why is Backflow Testing Important?
Backflow testing is crucial for protecting public health and ensuring the safety of drinking water. Regular backflow testing is a simple yet essential step in maintaining a safe water supply and preventing contamination that could endanger both public health and infrastructure.
What is Cross-Connection?
A cross-connection is any actual or potential connection between the public or consumer’s potable water system and any non-potable source or substance that present a hazard to the quality of the public or consumer’s potable water system. Therefore, cross-connection control is the management or “control” of these cross-connections to protect public safety by preventing backflow incidents within the public or water consumer’s potable water system.
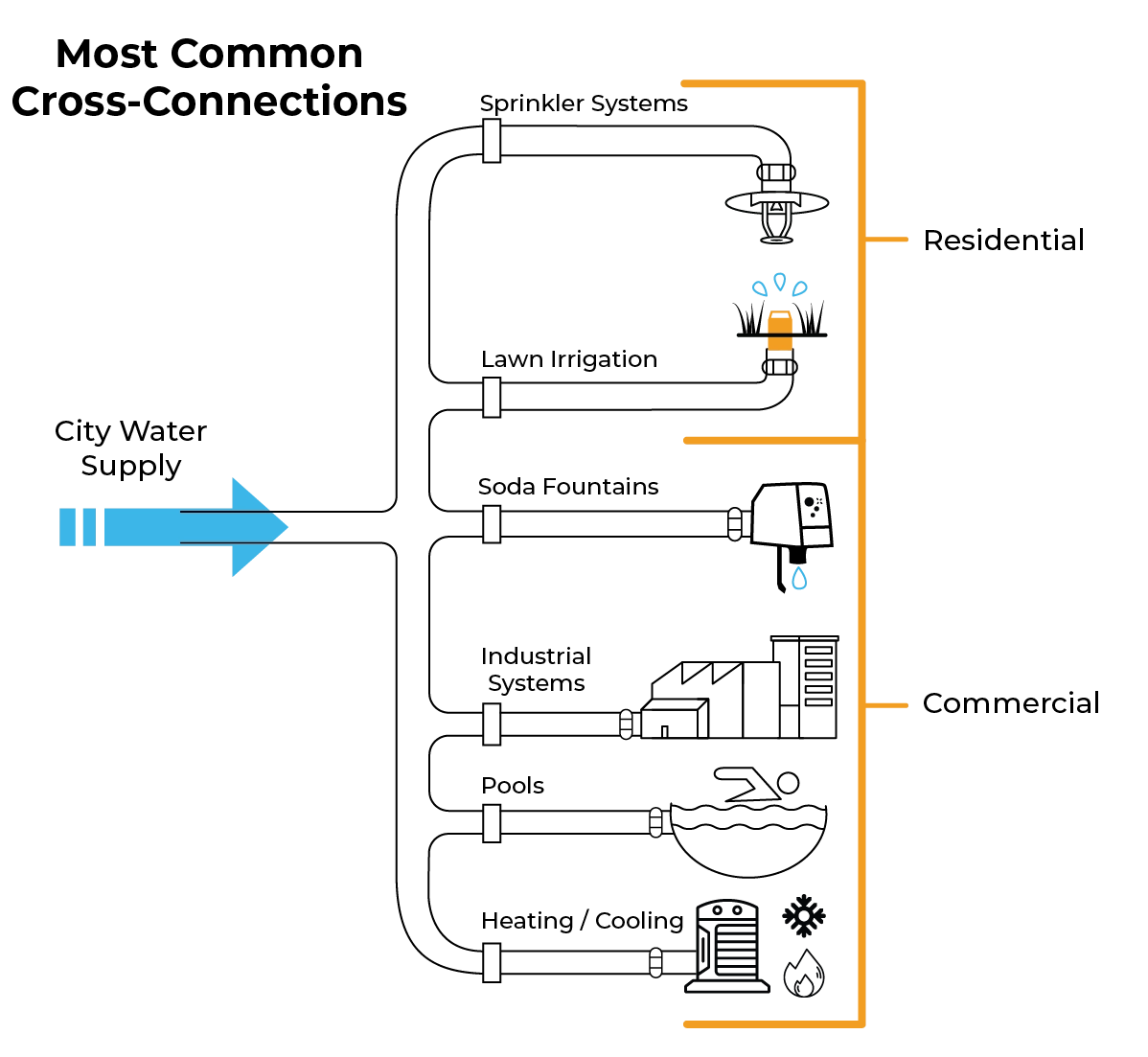
How are Cross-Connections Protected to Prevent Backflow Incidents from Occurring?
Ensuring the prevention of backflow incidents is crucial for maintaining water safety standards. Protection against cross-connections relies on two primary methods: containment and isolation. The most effective strategy involves a balanced combination of both containment and isolation measures, working together seamlessly.
Containment safeguards are strategically placed at the consumer’s water service or meter. This robust defense system covers the entire facility, effectively shielding the public water supply from potential contaminants lurking within the consumer’s plumbing system. However, it’s essential to understand that containment measures focus solely on safeguarding against external cross-connections and may not address risks within the facility itself.
In contrast, isolation methods are deployed within the consumer’s facility. These proactive measures serve as internal safeguards, precisely identifying and isolating hazards at specific points of use. By doing so, isolation measures offer comprehensive protection to individuals within the facility, preventing the infiltration of contaminants or pollutants into their internal plumbing systems.
Do Backflow Incidents Really Happen?
YES!
Are All Backflow Incidents the Same?
No, depending on the non-potable source or what the substance is, cross-connections are generally classified as high hazard or low hazard. Since there is no consensus, standards for defining and differentiating between a high and low hazard, each state (and on occasion the local public water supply) will define for themselves the criteria for each hazard. However, there is a commonality among the definitions.
What Causes Backflow Incidents to Occur?
Backpressure
Backpressure is created when the pressure within the customer’s system becomes greater than the water supply pressure. Elevated tanks, heating systems and booster pumps are some of the main causes of backpressure.
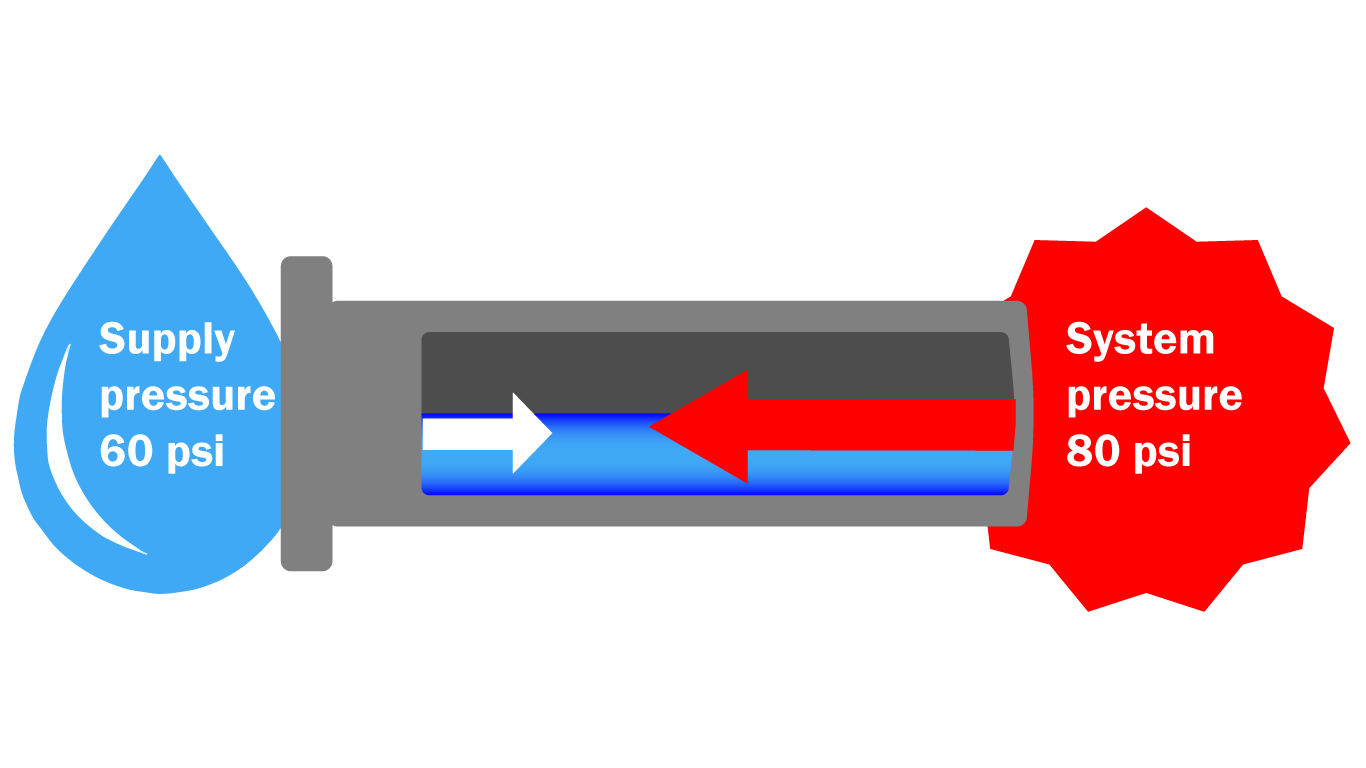
Backsiphonage
Backsiphonage is created when there is a negative or reduced pressure in the water supply main. Water main breaks or hydrant flushing are two of the main causes of backsiphonage.
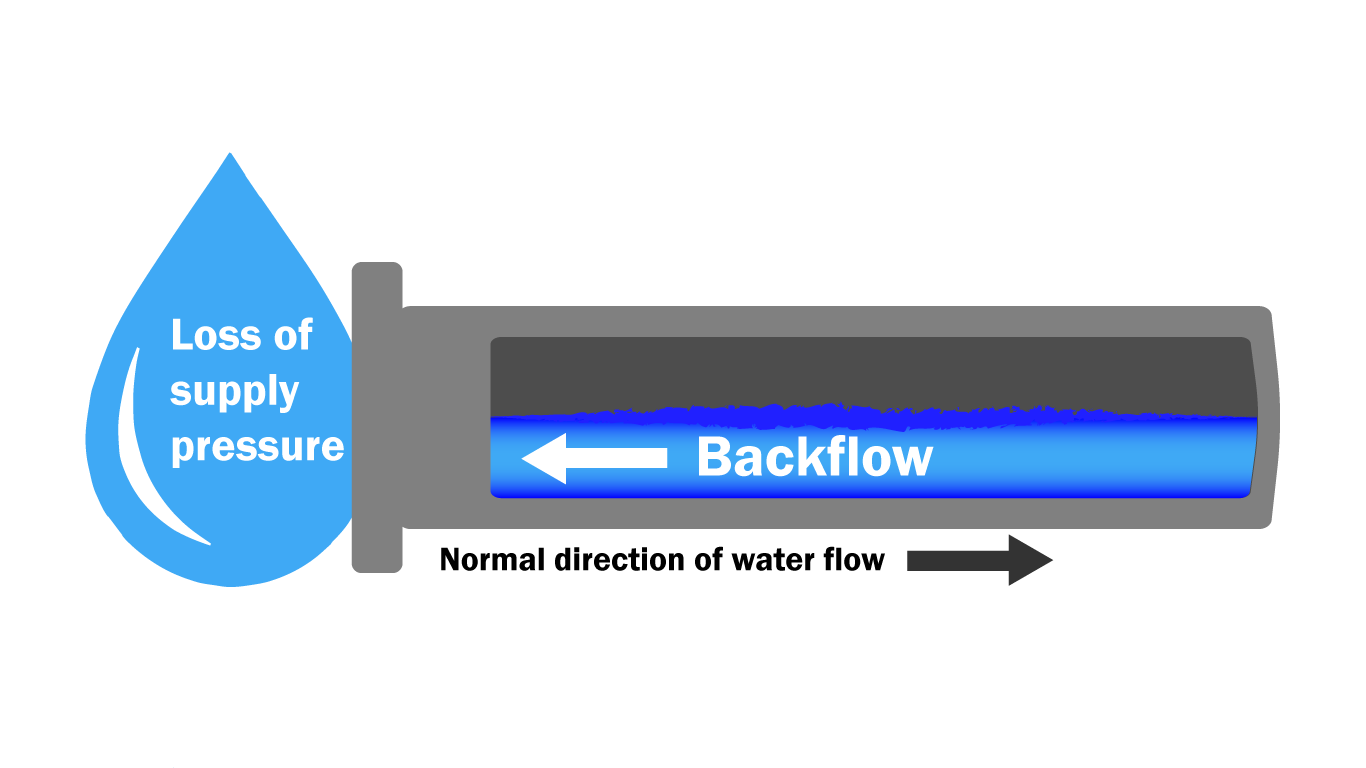
How can you Prevent Backflow Incidents?
Backflow Assembly Testing FAQ
Everyone involved in backflow prevention, including the water purveyor, local plumbing authority, water consumers, and those performing installation, testing, and repairs, shares responsibility in maintaining a successful cross-connection control program. Here is a breakdown of each imperative role:
Water Purveyor’s Responsibilities:
- Develop and enforce an ordinance that complies with state cross-connection regulations.
- Conduct on-site facility surveys to identify hazards and determine the necessary backflow protection.
- Keep detailed records of all surveys and maintain an inventory of backflow assemblies (and devices, in some areas).
- Create a testing schedule for all backflow assemblies.
- Notify water consumers when their assemblies are due for testing.
- Collect and store all test reports.
- Take enforcement action if there is non-compliance.
Individuals Installing, Testing, or Repairing Backflow Assemblies:
- Must have the required credentials to install, test, and maintain assemblies.
- Ensure testing equipment is properly calibrated.
- Follow the correct procedures for testing and repairing backflow assemblies.
- Accurately document assembly details like hazard, size, make, model, serial number, and location.
- Record the results of each backflow test and submit reports to the water purveyor on time.
- Provide a copy of the test results to the water consumer for their records.
Local Plumbing Authority’s Responsibilities:
- Implement and enforce local plumbing codes to ensure cross-connection control.